Associated General Contractors (AGC) and FMI recently published a survey of contractors’ perceptions of risk together with an analysis of factors expected to drive change in the U.S. engineering & construction (E&C) industry in the coming years. See Managing Risk in the Digital Age. The survey (completed late 2017 and published in 2018) yielded in four key findings:
- The “people factor” remains one of the biggest risks for E&C firms in today’s business environment.
- Industry stakeholders expect to see more change in the built environment within the next five years than there has been in the last 50 years.
- Most survey respondents are innovating “around the edges” and adopting technology in a piecemeal fashion (or not at all) but not fundamentally transforming their business approaches.
- For years, contractors have tackled risk by purchasing insurance programs and managing claims. Today that is no longer enough.
The survey notes that business is strong and is expected to continue well into 2019. Despite the current positive activity, E&C industry leaders are concerned with a variety of risk factors including: labor shortages (especially skilled trades and field supervisors but including managers), the decline in the quality of design documents, and the accelerating pace of technological change. These and other factors combine to increase the need for cross-disciplinary risk management.
The Acceleration of History
It is well known that the construction industry has historically been slow to adopt new technology. My favorite example is the pneumatic nail gun, which was used for wood pallet repair at least as far back as the 1960s, but not in construction. It was not until the early 1980s, that the production framing crews I managed in New England had fully adapted this “new” technology.
One surprising finding of the survey is that 58% of “industry stakeholders expect to see more change in the built environment within the next five years than there has been in the last 50 years.” The report contrasts how the Apple iPhone and Amazon were able to completely and surprisingly disrupt the cell phone, digital camera, and retail markets over short timelines. (Interestingly, this week marks the entry of Amazon into the $1 trillion market cap club, following closely in Apple’s footsteps.) The survey explores whether the sizable venture capital now available for digitization and disruption of the economy will make inroads into a traditionally conservative business. The authors highlight the arrival of E&C disrupters such as Katerra, describing its business model as similar to Toyota – fully integrated from architectural design through fabrication and installation.
In any event, change is looming in the construction industry. Current skilled labor and experienced manager shortages as well as flat-lined productivity improvements may prompt accelerated consideration of automation (e.g., robots, assistive exoskeletons). In addition, because a stunning 92% of E&C respondents reported that design documents provided to them are less complete than in the past, E&C firms are bringing more design capacity into their operations.
Technology and Uneven Disruption
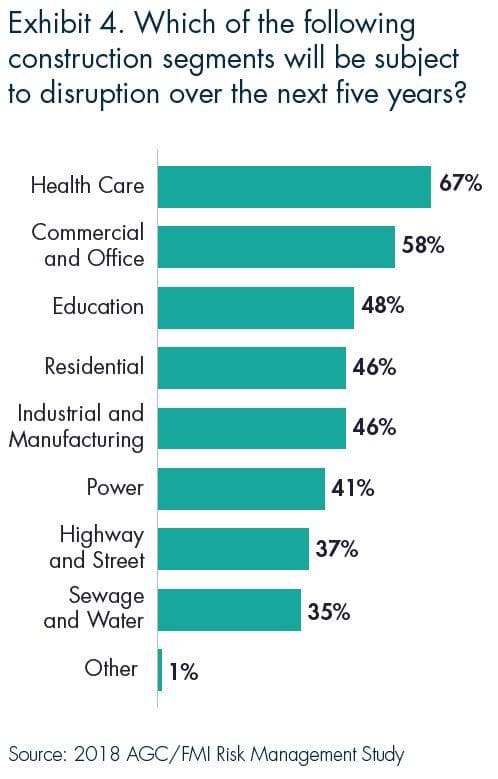
We now accept the fact that almost everyone uses texts, emails, and social media to communicate. Cloud computing, which allows workers to have current synced copies of manuals, contract documents, MSDSs, and other information, is now accepted as normal. For better or worse, everyone brings a computer and digital camera (in the form of a smartphone) to work every day.
Despite the flow of technology into all reaches of life and the workplace, transformative technological change in the E&C industry is slow. The survey finds that industry transformation is uneven across market sectors and geographies prompting E&C firms in the health care sector to build components offsite under controlled and automated conditions. This type of “constructuring” process was pioneered by Boeing and others using early versions of CATIA 3D software. Boeing’s Everett plant successfully assembled air frame components that had been manufactured to extremely tight tolerances by remote subcontractors across the globe. “Constructuring” is also the term for the method used to build the ISS. If it works well in the air and in space, it might bring productivity and cost savings to earthbound construction.
To build its new Sutter Van Ness Medical Office Building, for instance, Sutter Health is manufacturing and assembling seven of the building’s nine floors (equaling approximately 158,000 square feet of space) entirely off DIRTT, a proprietary 3-D software used to design, manufacture and install fully customized, prefabricated interiors. “Part of the reason we chose to go with DIRTT is we believe its approach can collapse our schedule by three to four months on the job site,” Michael Shanahan, a Sutter Health senior project manager stated in a company press release. “That alone means approximately half a million dollars in savings.”
2018 AGC/FMI Risk Management Study
Constructuring of laboratories and clean rooms likely saves time and money. It might or might not raise difficult risk management and legal issues. For instance, to what extent is a “fully customized, prefabricated interior” module a fixture (governed by the Uniform Commercial Code) or the work of the project (governed by common law)?
Construction Industry Slow to Adopt Digital Transformation
Despite the exploding end-user adoption of digital tools such as tablets, smartphones and apps to supplant traditional communications, recordkeeping, and other business tools, industry adoption of digital tools is hampered by lack of budget and C-Level understanding of the transformative opportunities presented by such tools. The AGC survey cited another report by JB Knowledge that identified severe shortcomings in the E&C industry:
- 46% of respondents have an IT budget of less than 1% of annual sales volume.
- Almost 13% of respondents don’t know the percentage spent on IT.
- Only 50% of survey respondents have a dedicated IT department.
These studies and other data suggest that the E&C industry is only innovating at the periphery of its traditional operations and business models. The high direct cost of implementing software and the mixed track record of IT solutions that don’t deliver have combined with skeptical conservatism to create change management fatigue.
Another observation is that the industry may provide ripe opportunities for cross-disciplinary approaches to IT and the built environment. Without IT savvy people who also understand the difficult-to-optimize challenges of building in the real world, it is difficult to make the business use case to executives for the transformative adoption of new technology and business processes.
Enabling Technology as a Risk Management Tool
After highlighting the lack of robust transformation in the E&C and the growing un-insurable risk, the survey makes a number of solid (yet still conservative) recommendations for adoption of digital technology:
- Develop a technology strategy that aligns with actual business need;
- Solutions should be scaled to the need;
- Pay attention to company culture and innovation fatigue when proposing change;
- Consider interoperability with industry partners and clients; and
- Pay careful attention to change management processes, including user training, documentation, and phased adoption.
Exhibit 8 from the survey provides a useful risk management matrix. While the matrix shows VDC/AR technology and PM Collaboration Platforms as checking off all or nearly all of the risk management boxes, the graphic is somewhat misleading. Project Management Collaboration is at the very core of the business need of every project. From a legal practitioner’s perspective, project management platforms improve documentation, aid ongoing communications, produce solid evidence as business records, and therefore mitigate risk. In my experience as a construction manager and later as a construction litigator, the project management and communications technology solutions would have a greater positive impact on risk management.
Going Bare: Uninsured Risks of Emerging Technology
In response to the risks created by increasingly incomplete design documents, E&C firms are providing more in-house design services. “Nearly 40% of respondence reported plans to bring design work in-house, and of those, over 80%have already completed this process or plan to have full in-house capabilities within the next three years.” Not only does this create the normal negligent design risk covered by professional liability insurance (E&O), the insurance products must additionally cover data losses, business interruption, data breaches (hacking), and privacy law associated with the digital data. It is no surprise that nearly 80 % of respondents expect insurance and claims costs to increase in the next five years. It is also notable that over 60% expect increased costs for dedicated risk management staff.
As E&C companies venture out of their traditional scope toward a cross-disciplinary or collaborative model, management and counsel should be careful to determine whether new risks are allocated by contract, insured or mitigated. The above chart lists 4 areas where Drone Tech can simplify project complexity and help mitigate risk. However, the survey also states that drones are frequently not covered under CGL policies. All new or changed risk vectors must be identified and categorized. Survey respondents readily admit that many of the new risks of collaboration may be difficult to insure. Risk management will instead need to focus on people, process, technology, and strategy of an organization.
Constructive Disruption
Business disruption is exciting – at least for the winners. Joseph Shumpeter’s “perennial gale of creative destruction” is evident wherever technology has been able to inoculate an industry. Tesla innovated away from the need for dealership networks. AirBnb disrupted the hotel industry and has upended the expectation of the enforceability of many land use regulations. Uber killed the golden goose of taxi medallions, while for a time leaving its “contractors” in the risky position of technically violating the terms of loan agreements and liability insurance on personal vehicles. Facebook’s credo, “Move fast and break things”, spurs innovation but it also may violate laws and cause real harms.
Joseph Shumpeter’s “perennial gale of creative destruction” is evident wherever technology has been able to inoculate an industry
Unlike the software industry where version 1.0 is routinely expected to have “bugs” or not work well, the built environment is not “virtual.” Real things that fail have real consequences, including personal or even criminal liability. Workers on construction projects are protected against harm by strict OSHA regulations; highway bridges such as the Route 63 bridge in Naugatuck, Connecticut are not expected to collapse as they are being rebuilt (as it did in 2010). Buildings are occupied by people even before substantial completion. The built environment is not supposed to fail.
Construction Risk Management began with the Codes of Hammurabi, where the law held a shoddy builder to strict liability if a person was killed – remedy = put the builder to death. In addition, the Codes stated: If a builder builds a house for someone, even though he has not yet completed it; if then the walls seem toppling, the builder must make the walls solid from his own means. E&C liability endures to this day in many forms, from failure to maintain bidder qualifications, to impacts on bonding capacity, to reputation, to enforcement of civil and criminal laws. Perhaps this real risk is at the heart of the E&C industry reluctance to disrupt itself too fast.